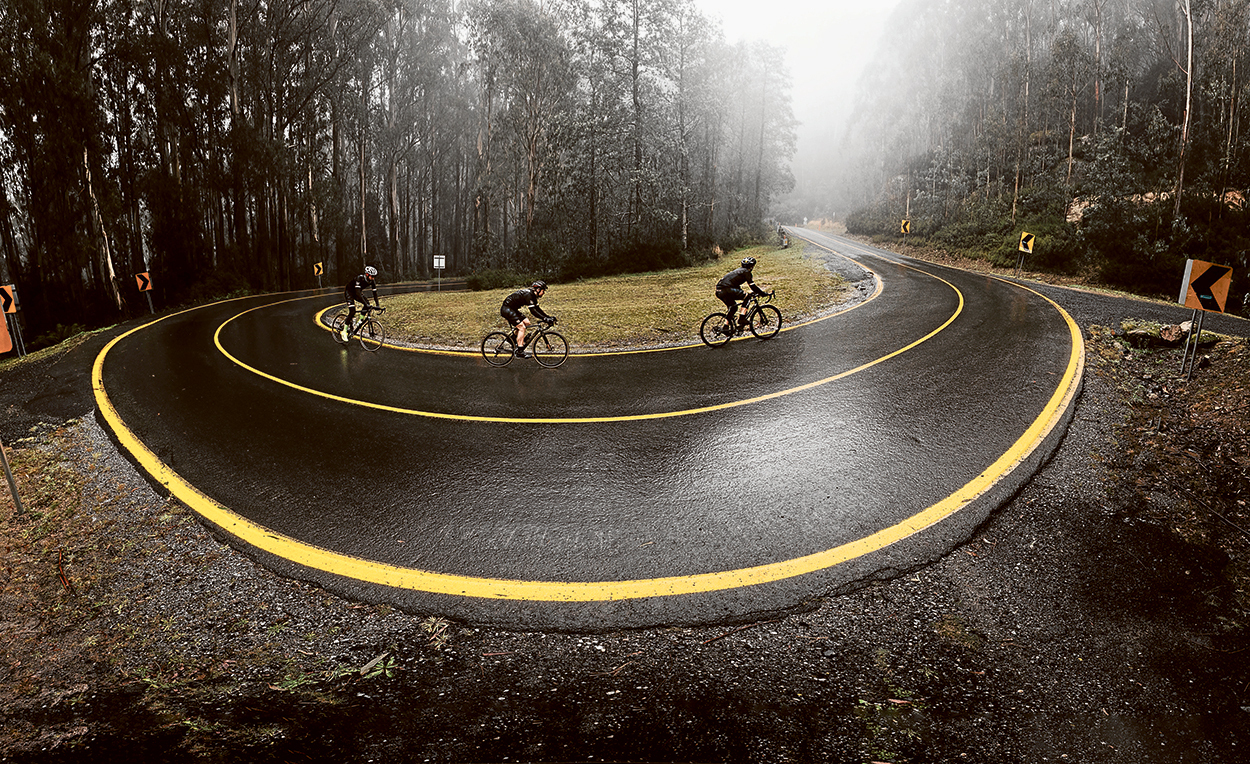
The inaugural Tour de Gippslandia.
Jul 19, 2017
Contribute to support more positive local storytelling.
SupportA number of Gippslandia’s team enjoy pushing pedals and lusting over opulent bicycles that their partners would never provide approval for purchasing — Bastion Cycles sleek carbon fibre frames and 3D printed aerospace grade titanium alloy lugs, make for no exception.
Whilst longing for world-class cycle gear may be a quiet passion of ours, it’s that Bastion was born as a proverbial phoenix rising from the ashes of the Altona Toyota factory closure that made us look closer. When 1200 workers were made redundant, Bastion’s three founders, Benjamin Schultz, James Woolcock and Dean McGeary, shifted the skills they’d acquired in the declining automotive manufacturing industry to high-performance bicycle fabrication. We had to know more, so we invited them to bring their best gear to ride our best hills; and with the Tour de France just weeks away, we launched the first Tour de Gippslandia.
—
But where to send them? — A quick conversation with lycra lover and former-Warragul sprint demon, Joel “Killer” Pearson, shared his wisdom on riding in the region:
“Gippsland is the ‘Mecca’ for cycling really. It has everything from the flat roads out past Longwarry to the steepest mountain climb in Australia. My favourite area for riding was the rolling hills between Warragul, Jindivick and Noojee. The climb from Neerim South to Jindivick was probably my most favoured route, as it stepped up (sometimes quite steeply) with great views back down towards Warragul and Drouin.
If I was up for a rush, you can’t go past riding down Red Hill (trying to nudge 100 km/h) or tackling some dirt roads over the back of Yarragon Hill in the Strzelecki’s. If you’re up for a challenge you have to head to Mt Baw Baw. It’s arguably the hardest alpine climb in Australia and some pros have said that it parallels anything in Europe for difficulty.”
That settled it. Bastion Cycles were heading up Mt Baw Baw in the inaugural Tour de Gippslandia — but not before giving us some intel on their background, technology and startup lessons...
Can you describe the ‘light bulb’ moment, when you thought that you were onto a great idea and a potential business?
We were still working at Toyota and I (Ben) “pitched” the idea to James and he accused me of stealing his idea! Turns out he’d already had the same idea and while I’d been working on the business model, he had already started designing a bike. It was the moment when we realised that it could work, both technically and financially, and that we were really onto something!
As you’re likely aware, the Latrobe Valley is in a period of transition, with some traditional industries declining. We understand you were in a similar position with Toyota before you created Bastion. How difficult was it to shift your mindset? Do you have any words of advice?
There’s a quote by Michael Jordan, “Don’t be afraid to fail. Be afraid not to try”. This is true if you want to take that step. You need to accept that failure may be the outcome. What helped us was realising that nothing is final. If Bastion fails, we still have the option of doing something else. I think humans tend to naturally be quite fatalistic about change and think that once you change, you can’t go back or change again, but of course, you can. That shift in mindset was key to overcoming our fears and giving it a shot.
Can you please describe the innovations that you’ve brought to bike manufacturing through Bastion?
Definitely 3D printing. Within that we’re innovating too; using a variable wall thickness as thin as 0.2mm and a structural internal lattice or honeycomb. This is innovative not just for bike manufacturing, but also for the automotive and aerospace industries. We’ve developed the world’s first free online bike geometry design platform too.
How does the ride on a Bastion bike compare to other road bikes?
The key feedback we get from customers is two-fold; how smooth and quiet the ride is, and how confident the handling is when descending. This is partly due to the custom fit and tailored geometry tuning of the bike, but also the torsional stiffness we achieve. The smoothness of the ride ensures the bikes hold their line, even through bumpy corners.
3D printing titanium sounds nuts! Can you please describe the process of additive manufacturing with metal to make your parts?
The process starts with a bed of very fine titanium powder, similar to the texture of talcum powder. A high-powered precision laser melts a layer of the shape. The temperatures can be 1300ºC! The machine then moves the powder bed down at the distance of the thickness of a human hair and spreads another extremely thin layer of powder over the top before repeating the process thousands of times until the build is finished. When heated titanium is highly reactive with oxygen, so the process needs to be done in a vacuum that’s then purged with argon gas. Once finished the excess powder is removed and the parts are heat-treated. Despite the image that 3D printing is “plug-n-play”, it’s actually a highly technical process and careful design considerations are needed to avoid distortion and failures, maximise the performance and improve cost effectiveness.
Given the wealth of engineering knowledge Gippsland, how does the region best capitalise on this knowledge? Is employing this talent in projects related to new, innovative manufacturing a good option?
As we neared the end of the automotive industry we recognised that the most feasible manufacturing in Australia is low volume, high value, niche products with global appeal and export potential – particularly sports and leisure products where “Made in Australia” carries substantial weight. One of the advantages of a high technology business is that it can be done successfully almost anywhere. Attracting talented staff can be difficult in regional areas, but it’s a big advantage if you have a local pool of technically minded and skilled operators. Our 3D printing supplier is in Tauranga, NZ (regional centre, 200km from Auckland). Traditionally a shipping port; active encouragement and local government support, has changed the area to a new technology park that’s home to some really innovative businesses.
Describe a ‘Bastion rider’?
Our customers are passionate cyclists who are ready to invest in something special and unique. We’re finding that we’re many of our customer’s first custom bike purchase. We craft something just for them; they can engage with us and be a part of the design process. Compared to traditional custom bikes ours are more modern, using advanced engineering and lightweight materials to achieving really impressive performance. Approximately 75-80% of our customers are overseas.
What are your goals for Bastion? Where do you hope to see the company in 5-10 years?
We’d like to be a world-renowned luxury cycling brand, building over 200 bikes per year, with a small, passionate and highly skilled team of 5-10 people. We want to stay small, agile and innovative. I also hope we will have been instrumental in helping to build an advanced engineering and manufacturing industry locally here in Victoria through our consulting work. We’re very passionate about helping others to transition and innovate as well and have been taking on some interesting side projects, not necessarily bike related.
Have you attempted to tackle the climb to the summit of Mt Baw Baw before?
Actually, none of us has ridden it. We’ve heard it’s pretty epic! The weather forecast is for snow at the top, so it will be interesting!